One of our first ornamental turning projects was making a series of pill bottles. They would be 2 ½ to 3 inches tall and 1 ¾” to 2” in diameter with threaded lids. Boxed in sets of 7, they would have different designs and be made from different woods. Since they were intended for practical use, a wood interior was not appropriate. So, the question of what would serve for a proper liner remained. There is, of course, nothing readily available on the market, so the liners would have to be produced in house. Fortunately, David has a hydraulic press and a deep drawing system from Bonny Doon Manufacturing
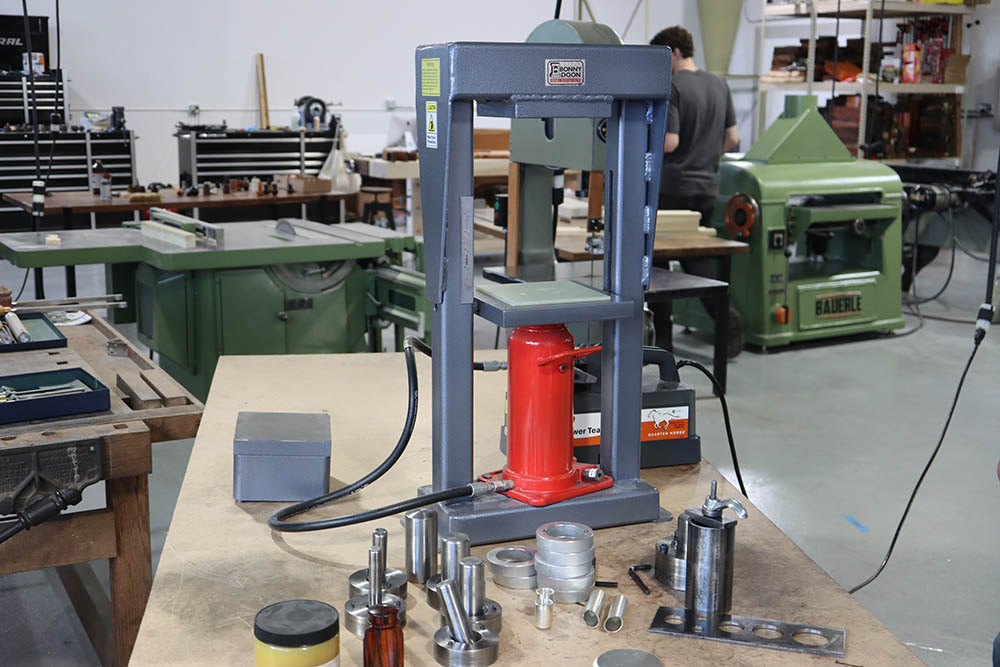
Wikipedia defines deep drawing as “a sheet metal forming process in which a sheet metal blank is radially drawn into a forming die by the mechanical action of a punch.” Until Phil Poirier, owner of Bonny Doon Manufacturing, made a system economically viable for the individual craftsman, deep drawing was restricted to mass production. According to Phil, the deep drawing process and press were invented in France around 1860 and quickly caught on. Manufacturers were soon drawing everything from cookware to buoys, anything that needed to be made in large numbers. (For the full article on deep drawing see his 2002 paper from the Santa Fe Symposium here) Before Phil’s system, the only two methods of making a tube or vessel such as we needed were by spinning it or raising it. Neither of these two methods are as precise as deep drawing, and either one would have taken a lot more time and effort. Drawing was the perfect solution. (See YouTube video of the process here)
Diagram of Drawing Process (courtesy of Bonny Doon Technology)
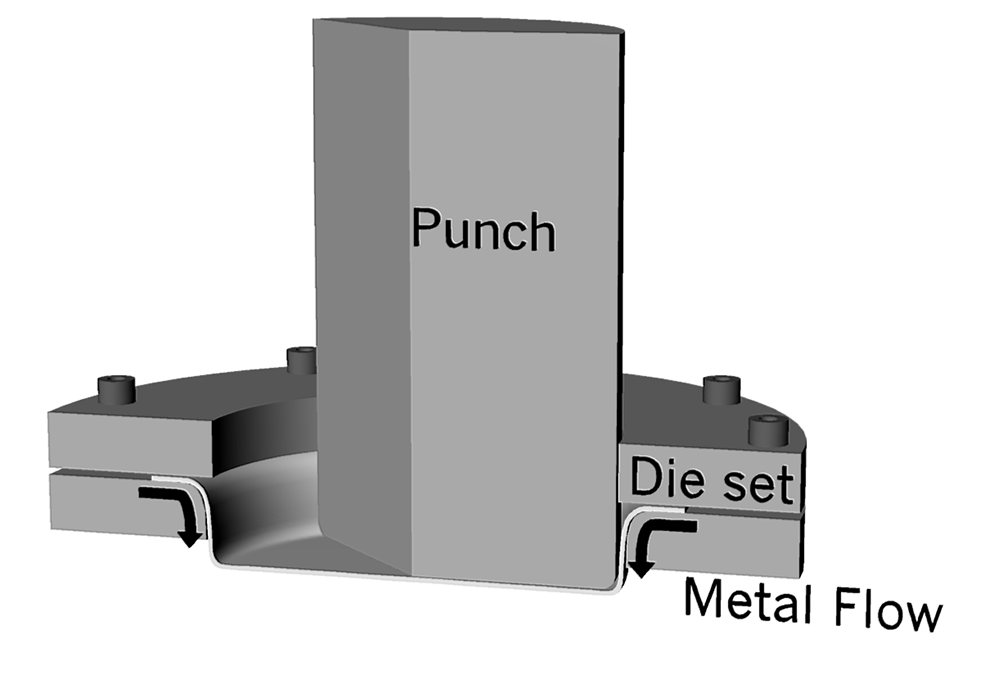
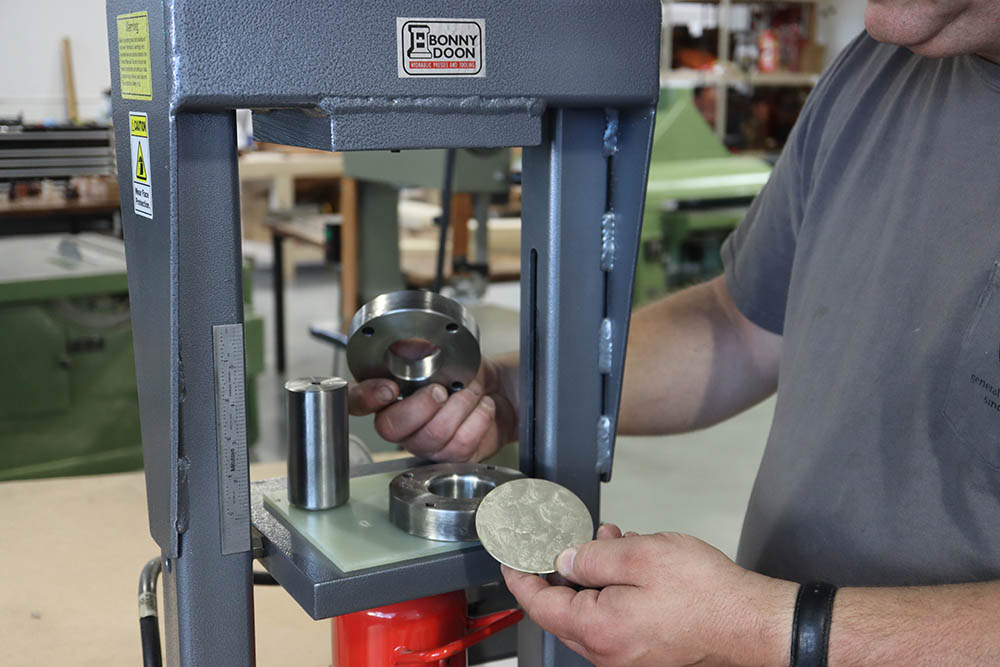
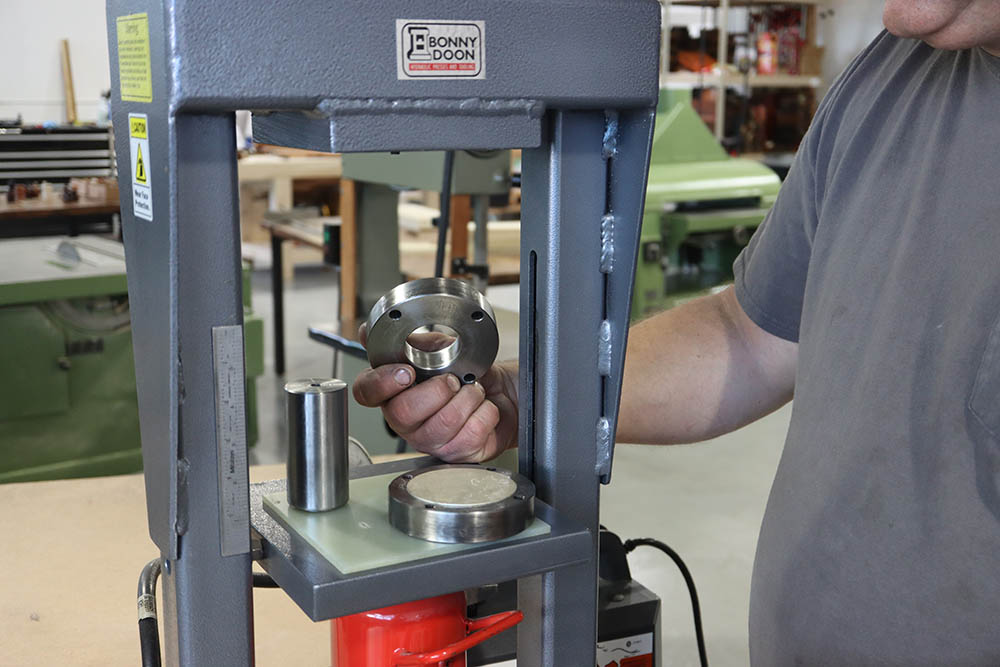
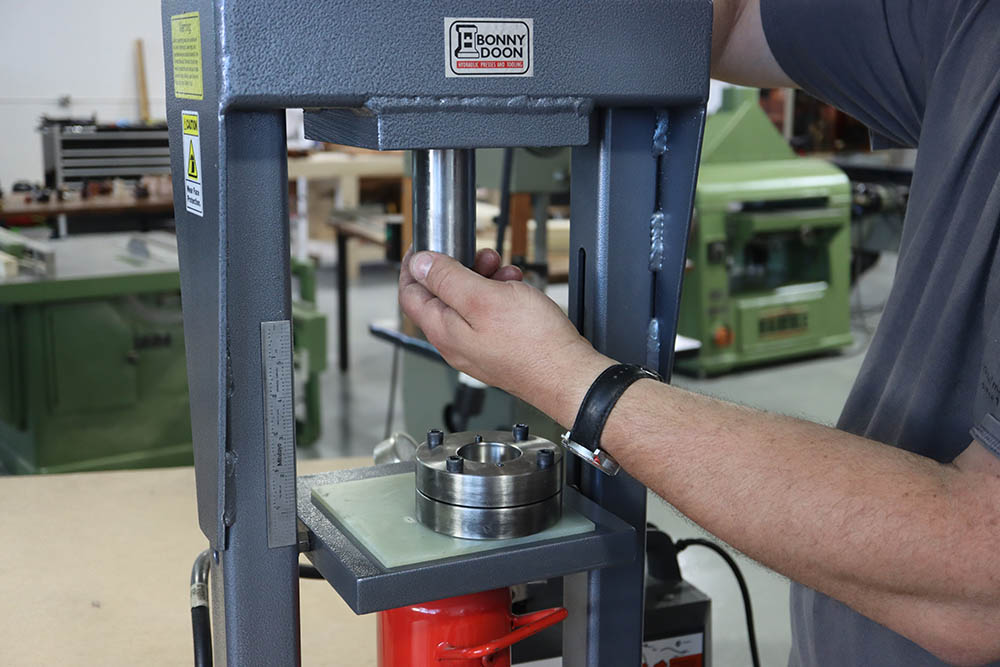
The die is placed on rings for clearance and the press is activated pushing the die upward and “drawing” the silver disc into a cup. The follower serves as a guide for the punch. Once the punch pushes the flat disc all the way through the die, a cup is formed. The punch and die are then removed from the press and the cup taken off the punch.
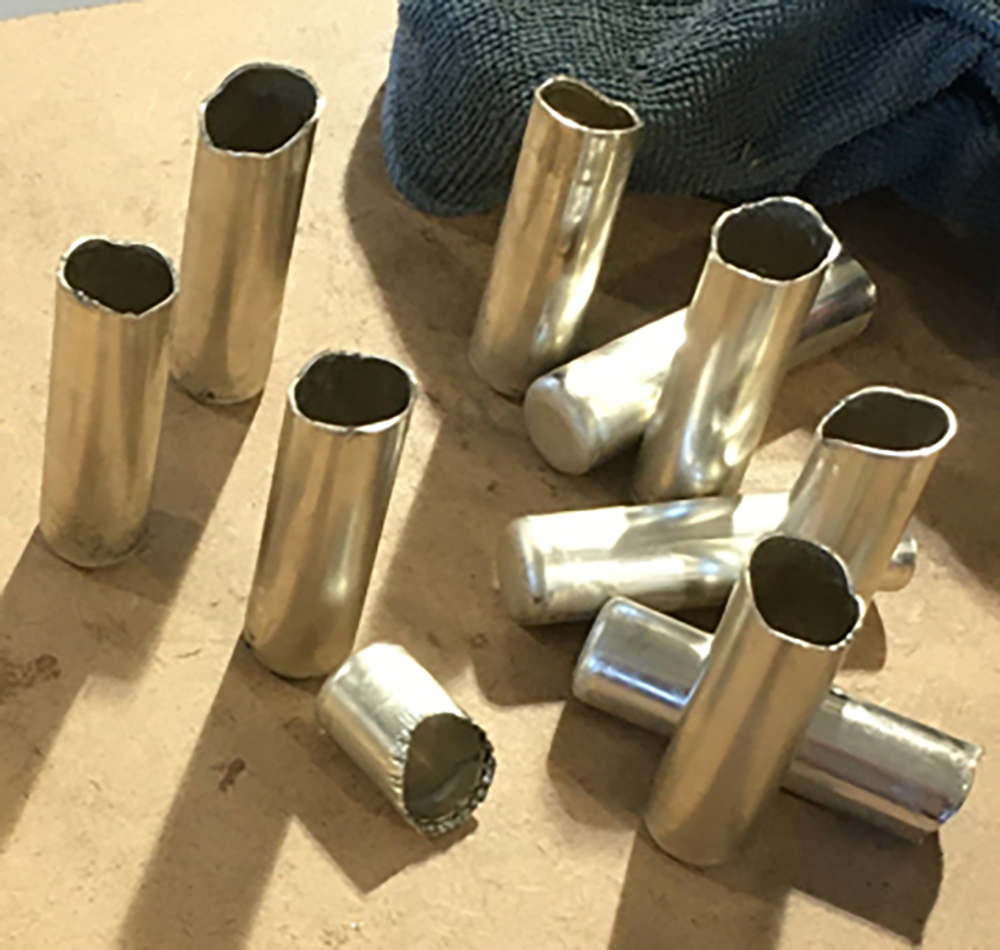
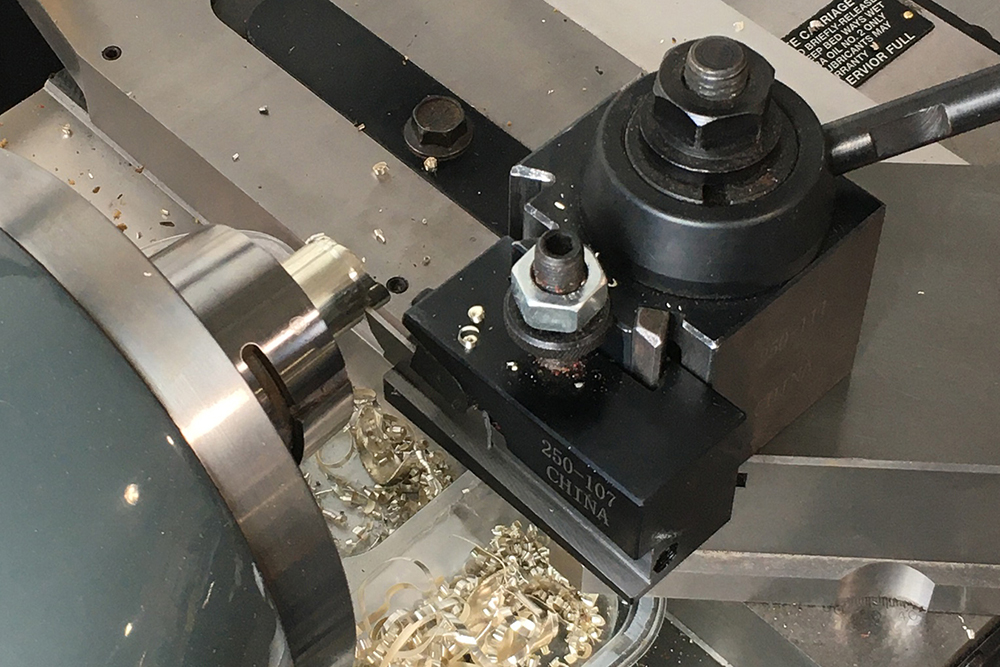
Since the tubes are all drawn to a precise diameter O-Rings were a perfect way of securing them inside the bottles. They could be removed if need be, but removing them would require an intentional effort to get them out.
After being parted off on the lathe, the top edge was too sharp, so the tube needed a smooth flange on its rim. We made a spinning tool to fit into the tool post of the Hardinge lathe and turned one of the prototype pill bottles into a spinning fixture. (See You Tube video here).
The spinning tool made to fit into the tool post of the Hardinge Lathe. The tool is essentially a clevis on a round shank so it can be set at an angle. A hardened steel wheel with a rounded and polished edge is mounted on an axle in the clevis. The tube is pushed into the spinning jig and held in place by O-Rings. With the lathe turning the roller wheel on the spinning tool forces the silver against the edge of the jig and begins to create a flange. The roller repeatedly pushes the silver over until it eases it against the end surface of the spinning jig. When it seats against the jig’s surface it is finished. Even with having to take a few passes, this process takes fewer than 20 seconds. The tube is extracted from the jig. Note the O-Ring and the radius on the inner edge of the spinning jig that softens the curve and keeps the silver from cracking.
Once the spinning process is finished, the flange is turned down to a precise dimension. Signing it before installation is the last step. Then the tube is slid neatly into its destination hole to become a gleaming liner for a pill bottle.
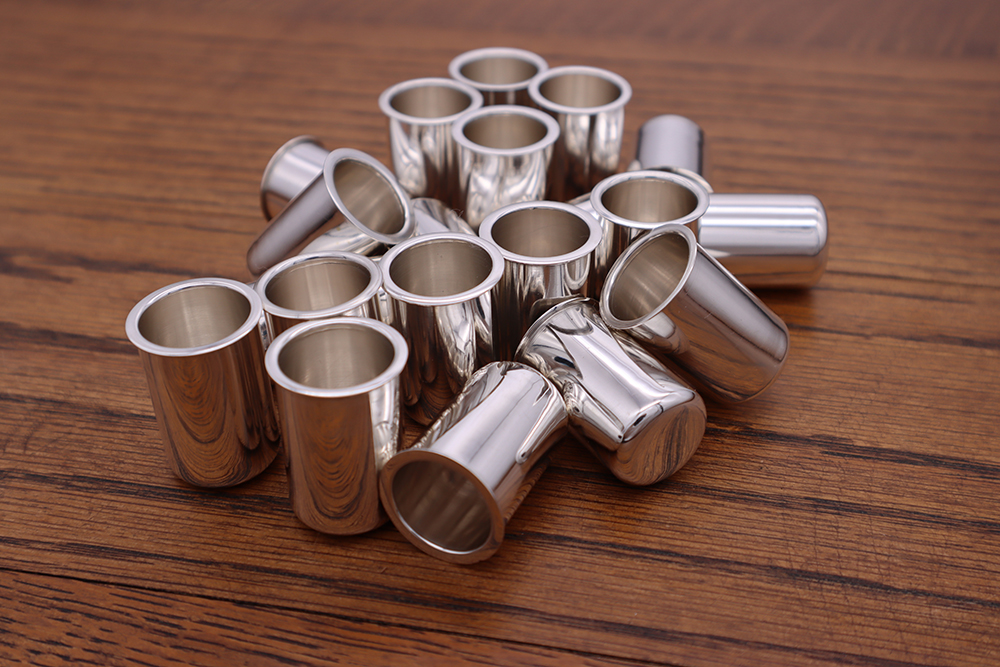