The shop at the Plumier Foundation is primarily a woodworking shop. However, one thing that sets the shop apart from many others is its machine shop. As unusual as that is, the machine shop was deemed essential. When Bill first proposed to David his idea of setting up an ornamental turning and cabinet shop, David immediately said, “You’re going to need machine tools to support the rest of the shop.” And when deciding what lathe would be needed for the machine shop, there was no question in in David’s mind. It had to be a Hardinge HLV-H-EM.
The last new Hardinge HLV-H lathe left the factory in 2015. (For more on the Hardinge click Here) However, Babin Machine, Inc. of Marshfield, MA rebuilds Hardinge HLV-H series lathes to better than new specs. Once the Plumier Foundation’s order was placed with Babin Machine, it would be some 16 months before its Hardinge lathe was ready. The Plumier Foundation took delivery of the machine in November of 2019, some 18 months after it was ordered. Great things take time. The lathe did not disappoint.
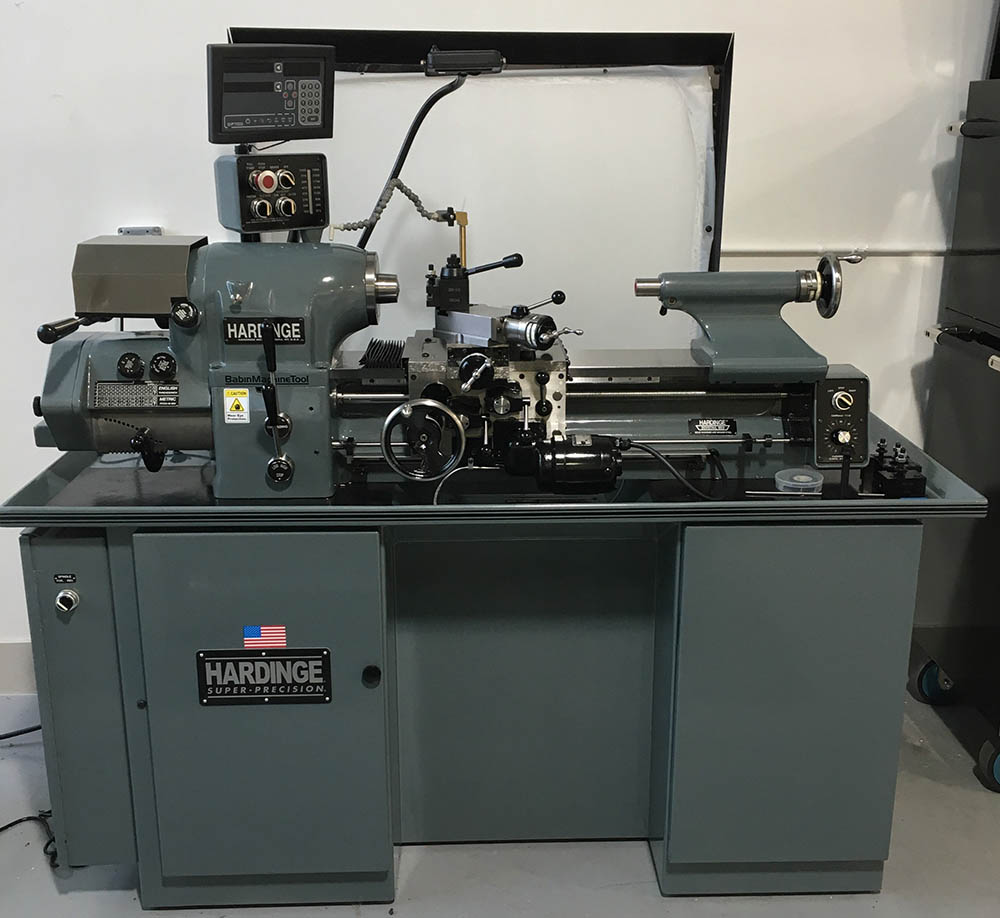
For those familiar with metal working machinery, the Hardinge lathe is nothing less than an icon. But this doesn’t tell the full story of just how competent and accurate these lathes are. Even someone as seasoned in the machine trades as David can’t get over the silky, almost frictionless action of the lead screws, the smoothness and quietness of the drive system, and the ease with which the tailstock glides along the wide bed, full contact way surface. The lathe runs so smoothly that a coin can be placed on the round top of the headstock, and it won’t vibrate off, even during a moderately heavy cut. The lead screw handles are works of art, as pleasing to the hand as they are beautiful. Form truly does follow function and when things are right you have it all. The Hardinge HLV-H-EM is truly a marvel.
Hardinge began to develop the HLV lathe in the mid 1940’s as a replacement for its ever-popular T-10 tool room lathe. While the T-10 had dovetail ways, it’s headstock and tailstock were aligned by means of the 60⁰ “split bed” design that was ubiquitous on bench lathes in those days. While some of the T-10’s better ideas were carried over, the HLV lathe which appeared in late 1940’s must be thought of as a complete makeover. In order to stiffen up the casting the split bed profile was abandoned in favor of a solid, wide dovetail bed that was hardened. Because both the carriage and tailstock ran on the same bed way, it was possible for them both to have full contact with the bed on their locating surfaces. Given that the bed was now hardened, the wear factors were exponentially reduced. Also, the new bed design had such smooth carriage action that even a machinist with a lifetime of experience will marvel at the ease with which so much mass is moved as the carriage handle is turned.
It’s always nice to introduce yourself to a new piece of equipment with a simple project. The first real project we did on the Hardinge was to make simple saw arbors for mounting circular jeweler’s saw blades in the Bridgeport milling machine’s spindle. The lathe exceeded even David’s high expectations, with the shanks of the arbors having so little run out or taper that neither could be detected with a .0001” micrometer.
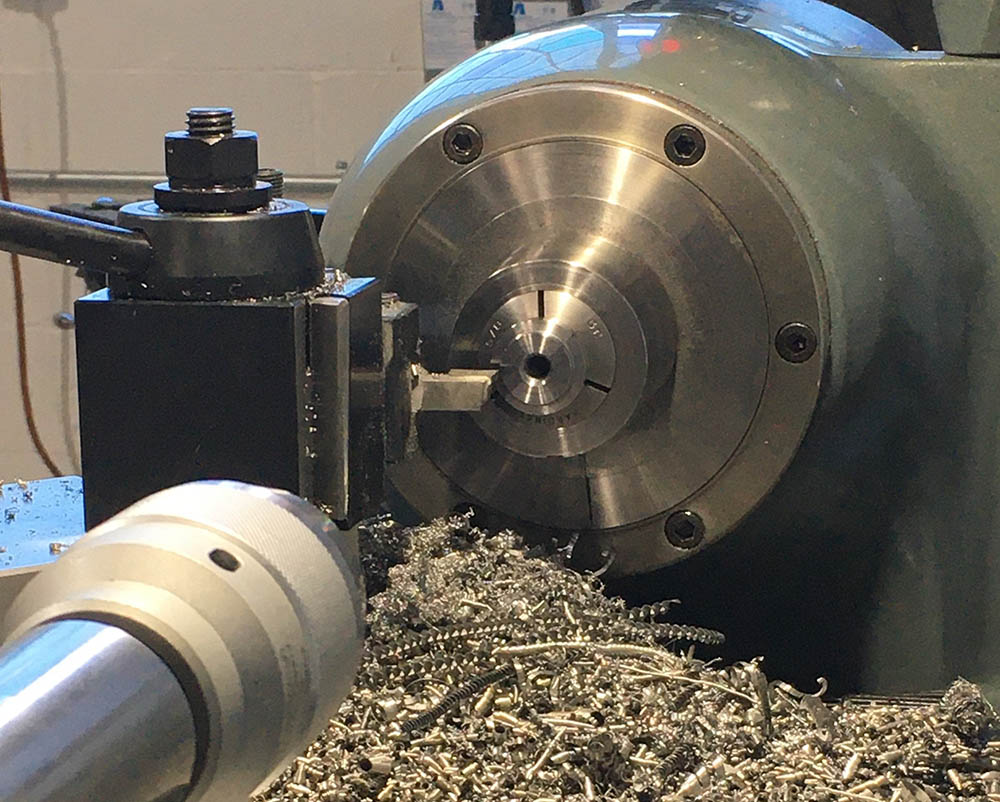
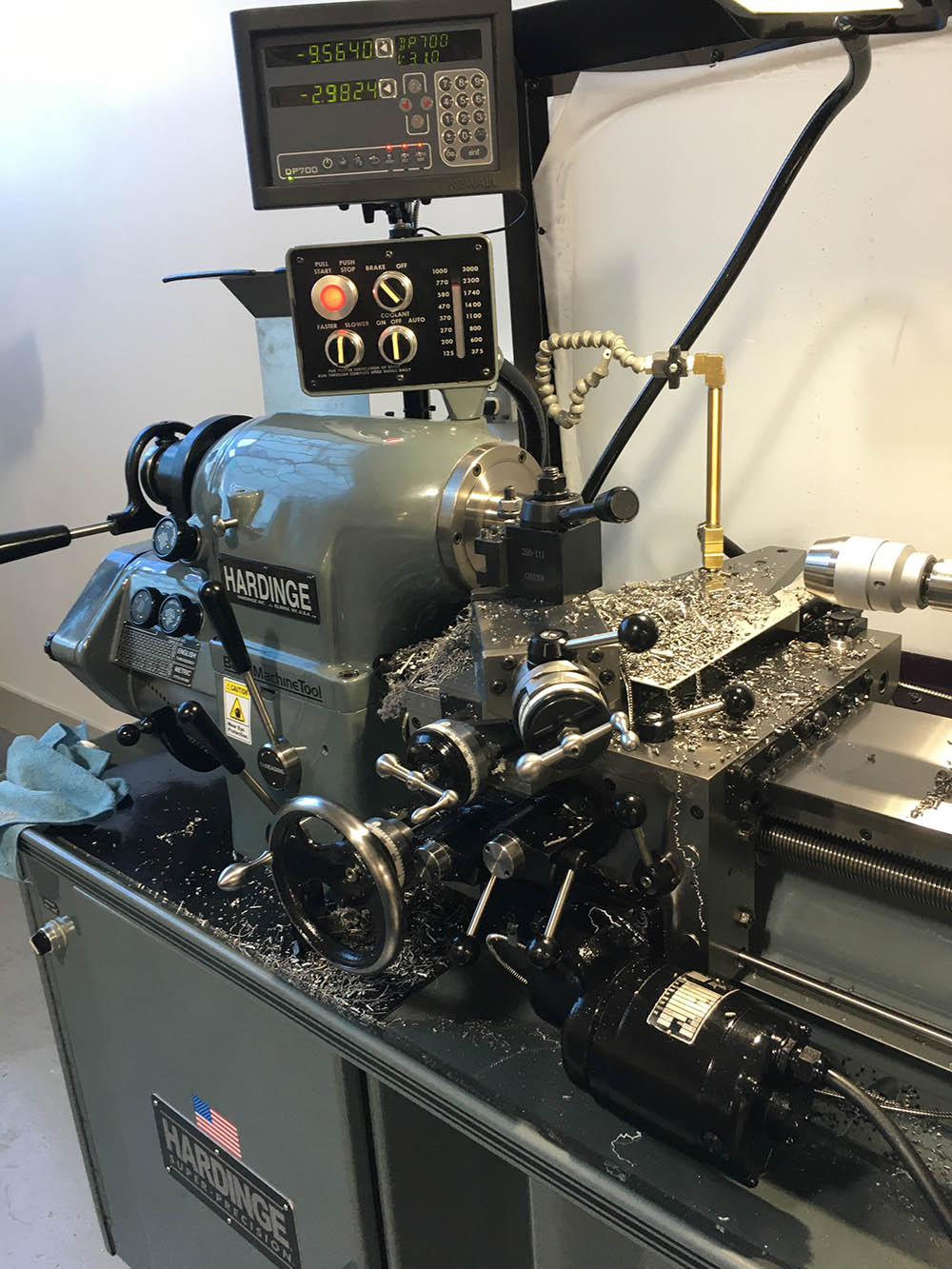
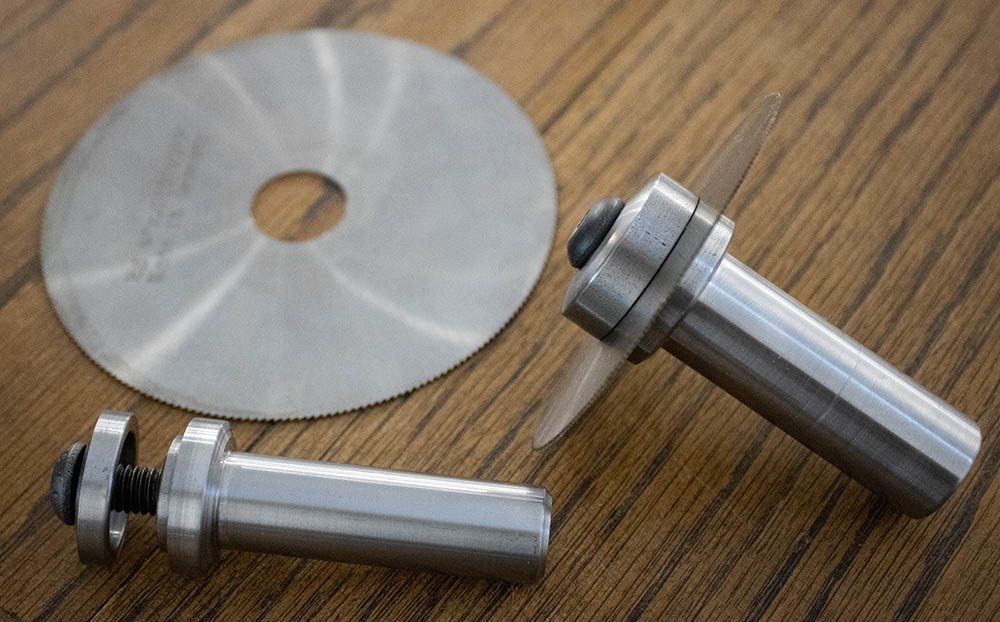